Autonomy ahoy: Shipping industry moves toward crewless vessels
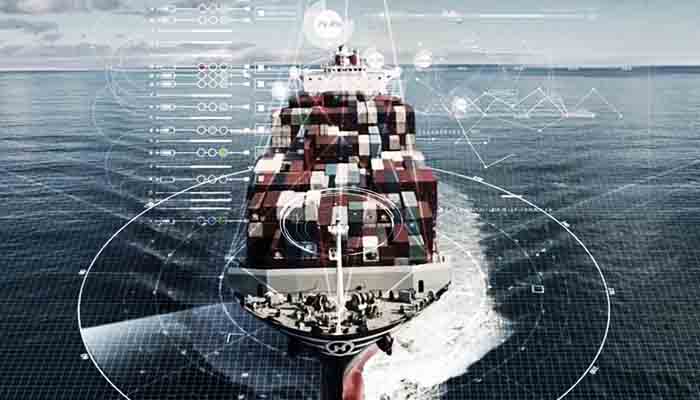
Autonomous vehicles have been attracting a lot of attention as the automotive industry pushes towards future mobility. But what is the potential for autonomous ships?
While the deployment of autonomous ships may be lagging behind the roll-out of self-driving cars, across the logistics industry companies are already laying the foundations for the introduction of the first autonomous fleets.
Promising the possibility of crewless cargo transport, fuel-efficient movement and accident-free operations, autonomous technology holds great potential and in some respects is already proven. Yet there may be a significant time lag before the first autonomous car carriers arrive.
From a shipping line perspective, cost savings and safety improvements offer tempting incentives, but the ways in which autonomous systems will interact with human control and the risks they pose in the real world are issues that are far from resolved.
“In general, from a commercial perspective the main benefit is cost saving, with a reduction in operational costs directly linked to reducing operational costs, but the major challenges and risks at present are all around safety,” says Bjørn-Johan Vartdal, head of DNV GL Maritime Research.
”We might see regular short-sea shipments by fully autonomous vessel in as little as five years, but I think adoption of the full technical potential for deep-sea traffic is likely to take at least 20 years” – Pia Meling, Massterly
“No crew on board would mean no risk to life and potentially increased reliability and predictability, with computer controlled systems not suffering from fatigue and human-related errors, and able to follow set rules and take decisions much faster,” adds Tim Rufus, general manager North America and Asia at Siem Car Carriers, although he concurs that car carriers are unlikely to be among the first vessels to feature full autonomy.
Vegar Bøthun, head of IT at Höegh Autoliners, also believes there is “definitely potential” in autonomous technology and draws parallels with existing automated operations in the oil and gas industry, plus automated landing systems on aircraft. He says that once the technology is fully proven, shipping operations will be “less error-prone” than those subject to “the human factor”.
Short-sea versus deep-sea
One clear distinction when considering the roll-out of autonomous vessels for the automotive logistics sector is the difference between short-sea and deep-sea traffic. While a limited number of autonomous car carriers may appear for short-sea shipment as soon as the next five years, there is a consensus that deep-sea traffic will take much longer.
“It seems more likely that automation will be better suited to certain trades and vessels. On car carriers, due to the cars being susceptible to movement in heavy weather, automated vessels do not appear to lend themselves, at least initially, to deep sea international trading,” Rufus explains.
Bøthun believes that routine autonomous shipping will take “another five to ten years, with an emphasis on the latter”. He says the technology will first be deployed for short sea, “then deep sea from buoy to buoy, where crew are picked up just like airlines send their crew around the world to fly with different airplanes on different routes”. He says this will open up ”greater flexibility” but also “many more variables to adjust, like competency and number of staff to match the cargo and voyage ahead”.
For deep sea, he says major difficulties facing the implementation of autonomous technology are that the machinery currently requires supervised maintenance and that cargo must be inspected in order to stay safely lashed. Another obstacle to automation is that “slow regulatory processes” mean the industry is not currently gathering and testing the necessary data.
Bøthun says Höegh is wary of trying to move “unrealistic barriers” in terms of both its own operational boundaries and external regulations, but that the company is “looking into different types of bots, to augment our crew in their day-to-day decision making as well as testing out various means to improve tracking of both vessels and cargo”.
”Automated systems can raise the crew’s awareness by offering decision support and help avoid accidents when a critical situation is detected” – Bjørn-Johan Vartdal, DNV GL
Vartdal of DNV GL agrees: “With short-sea shipping, while there is increased complexity due to proximity of land and of other traffic, it is compensated by good communications, which is important as a strong link to a remote operator is likely to be vital.
“When we look at deep-sea, the issue of remote assistance or disaster avoidance is of course more acute and on top of this the matter of international regulation makes the outlook more difficult. For these reasons, we are probably likely to see the first commercial autonomous vessels in short-sea shipping well before deep-sea.”
DNV GL began working on autonomy in 2014 and Vartdal notes that the field has “changed dramatically” since then, but despite the rapid improvement of intelligent systems in the last five years the promise of fully autonomous vessels remains an elusive goal.
Certification challenges
No matter how many tests are carried out or positive trials completed, there is always the danger of an unforeseen failure, and a future of accident-free shipping, with zero-risk to human life, is still far from certain until clear guidance and certification practices are in place.
“Autonomy will be a game-changer for the class societies,” says DNV GL’s Vartdal. “Traditionally, we have been involved in approving ship technology, but the operational part we’ve left to the crew. In autonomous vessels, the operation is embedded in the technology – it’s the software that decides how it will manoeuvre – so we will have to approve the safety of the whole operation. This is, of course, really challenging and it will have to be a case of continuous development.”
This challenge is currently being met through the pursuit of better data and standards, but instead of turning to real-world trials, some agencies such as DNV GL are taking their lead from the way extreme weather events are predicted and relying on computer simulations to forecast outcomes instead.
“It is very difficult to ensure safety at present, given the lack of data available and the inability to account for sufficient conditions through real-world testing,” explains Vartdal. He says DNV GL is pursuing a simulator approach “where we simulate multiple cases and use this data to test the systems reactions”.
Norwegian joint venture Massterly is one firm chasing this goal and it is already planning the launch of its first autonomous vessels for short-sea voyages. Publicised as the world’s first full-service autonomous shipping company, the firm is a joint venture between Norwegian shipping specialist Kongsberg and shipping and logistics group Wilhelmsen, part-owner of car carrier Wallenius Wilhelmsen Ocean.
“We might see regular short-sea shipments by fully autonomous vessel in as little as five years, but I think adoption of the full technical potential for deep-sea traffic is likely to take at least 20 years,” says Pia Meling, vice-president of sales and marketing at Massterly.
“The main reason for this is regulation, as it is feasible to get approval for reduced crew or unmanned operations within one nation or a cluster of neighbouring states but it will take far longer for IMO [the International Maritime Organization] to develop adapted regulation covering all international waters.”
As soon as next year, the world’s first commercial and fully autonomous vessel will be launched as the electric container ship, Yara Birkeland, is delivered from Vard in Norway.
The vessel is owned by fertiliser company Yara and will be operated by Massterly’s shore-based crew while the vessel itself well be unmanned, after a testing period with reduced crew onboard. Measuring 250 feet (76 metres) long and capable of carrying 120 containers, the vessel will operate in Norwegian waters. It will act as a bellweather for future development.
“There has been a lot of research and prototypes but we will be the first to launch a commercial fully autonomous vessel, replacing the equivalent of 40,000 trucks yearly,” claims Meling.
Steering clear of stormy weather
One key factor mitigating against deployment of autonomous car carriers is the likelihood of extreme weather conditions in ocean transit.
“There will be increased costs from risk of damage to cargo or the vessel in transit, for instance if cargo shifts during heavy weather due to failed or loosened cargo lashing,” Rufus of Siem states, adding that this “could be catastrophic and even cause the loss of the vessel for car carriers”.
Related to the risk of damage to the vessel itself is the fuel choice for propulsion. As Meling points out, vessels today require a chief engineer on duty, mostly due to the risk associated with fuel oil and combustion engines.
“If we transition to fully electric, battery-powered vessels a lot of this risk, and the need for onboard maintenance, is reduced,” Meling says.
”The safety and regulatory environment is not currently set up to accommodate remote controlled or autonomous vessels” – Tim Rufus, Siem Car Carriers
Electric power also offers easier integration with electronic systems and superior data monitoring potential, but while battery technology exists today it is still far from ready for widespread commercial deployment. This is particularly true in the case of deep-sea transit and as such, Meling expects roll-out of fully autonomous vessels to require greater maturation of battery technology as well as transition to zero-emissions fuels like hydrogen.
“Automation could be better suited to river or coastal vessels where the environment can be controlled, vessels can seek shelter and also use simpler propulsion systems, such as battery/solar-powered electric motors, which can be maintenance-free,” Rufus suggests, adding that even then it is “unlikely that these vessels will be cost-competitive with conventional vessels, without significant funding and grants being made available.”
Reducing human crew
Although the complete removal of crew from deep-sea vessels is unlikely to happen in the near-term, a rethinking of vessel design may allow for crew reduction or novel configurations, such as temporary handover to intelligent systems.
“One key development we are likely to see in the short term is the increased occurrence of a periodically unmanned bridge, where automated systems take over control from the crew on a temporary basis – allowing crew to sleep or complete other tasks and reducing the need for crew redundancy onboard,” Meling predicts.
Such an approach is expected to have multiple benefits beyond the simple reduction of crew costs. At present, crew handover periods are a major locus for human error and accidents, so it is hoped that intelligent systems may be able to help.
“Many shipping incidents are related to the crew being inattentive. Automated systems can raise the crew’s awareness by offering decision support and help avoid accidents when a critical situation is detected,” says DNV GL’s Vartdal. “They could also facilitate partially unmanned operation by recognising when another ship is on the radar that might cause a collision, and alert the crew. In time the system could also change the course and contact other vessels.”
On the other hand, trusting decision support systems too much could lead the operator to become inattentive and therefore in itself compromise safety. This risk is something that ship operators need to determine.
A further advantage of temporary control of autonomous systems while a full crew is still onboard would be to allow companies to gather valuable data without having to risk sending fully autonomous vessels out unsupervised.
Rufus of Siem points out that a smaller crew can deliver significant savings not only in direct payroll but in reduced training, facilities, accommodation and other ancillary costs of employment “such as victualling or crew mustering costs”.
“Shipping should be in the forefront [of autonomous technology] and take advantage of the efficiency gains, cost savings as well as the safety and security opportunities that are there to be harvested” –Vegar Bøthun, Höegh
Not all these changes may be positive for the bottom line of shipping firms, however. Rufus goes on to note that: “Crew maintenance and shipboard operations will need to be condensed into port stay. There may be increased costs for stevedoring and shore-based maintenance gangs or riding squads, as well as increased office cost for additional planners and office-based vessel operators.”
Whereas abstract discussion of temporary autonomous systems frequently considers vessels with fewer crew on board, the reality is that most ‘autonomous’ vessels, will, at least in the first instance, require even more crew.
“We are investing heavily in redundancy and security for these first vessels as it would be a reputational disaster if we fail in this early stage of building public trust in the autonomy technology,” Meling says.
Autonomous tech and cybersecurity
Cybersecurity has already become an issue in the shipping industry, with cases of criminals hacking radar, bridge control and information systems. Höegh’s Bøthun points out that this is “both a security as well as a safety issue that must be dealt with”. He believes that the necessary safeguarding actions are similar to land-based cyber defence.
“It’s about training, good IT security practices like strong password and routines, two-factor log-in, network segregation and encryption of data at rest, in memory and in transit. It’s about collaborating within the industry and across industry against the fraudsters to make it as difficult and unattractive to conduct cyberattacks as possible,” he states.
Yet as more decision-making processes on board a vessel are transferred from human operators to silicon circuits, the risk of malevolent agents hacking or taking control of a ship is set to increase.
“With the growing reliance on electronic devices and software systems, cybersecurity will always be a risk. The risk will only grow as automation increases the reliance. Shipping lines will need to instil a culture of cyber risk management and have systems in place to counteract the risk. We have seen more focus on cybersecurity from the likes of the IMO,” Siem’s Rufus states.
Given recent moves by the US to blacklist Chinese equipment manufacturer Huawei over national security concerns, geopolitical tensions may also influence the development of future autonomous vessels.
On the other hand, there could potentially be a reduction in certain types of attack due to the removal of crew and the ability for remote operators to override manual controls, rendering the vessel secure.
“Most cyberattacks that are successful have entered the IT systems through a human clicking on an infected link or using a malignant USB stick, so ships that have nobody onboard are far less prone to attack,” Meling notes. She adds that there would be less incentive for traditional piracy due to the limited opportunity to take control of the vessel – and zero possibility of taking hostages for ransoms.
“We are building in the ability to put the ships into ‘safe-mode’ remotely should any unusual behaviour be detected, and fully autonomous vessels as well as score control centres are constructed with cybersecurity in mind for every component,” says Meling.
Despite these advantages, the current state of hull and machinery or protection and indemnity insurance contracts means that work still needs to be done before indemnification can be achieved.
“At present, one of the major challenges for the next iteration of autonomous ships is the development of a machine-readable version of COLREG, or the rules of the sea,” says Vartdal. “DNV GL is already working on initiatives to turn the current regulations into a form that machines can understand and use. This is a vital first step if we are to understand and safeguard against the various legal and regulatory difficulties that are likely to develop when autonomous vessels start interacting with each other on a mass scale.”
Avoiding collisions
Feeding into the desire to overprovision for safety in the first autonomous vessels is a lack of accurate data about the operation of autonomous vessels in real-world situations. While driver assistance is relatively easy to implement, the improvements car carriers may stand to gain by reducing human error become far more complex when human control is taken away entirely.
One obvious danger of completely unmanned vessels is the possibility of collision. An industry-wide research initiative, the Dutch Joint Industry Project Autonomous Shipping, is currently conducting trials in this area.
Bringing together 17 key players from industry, government bodies, knowledge institutions, classification societies and pilot organisations, the project is examining the groundwork necessary to begin deployment of systems in real-world situations.
In March 2019, the consortium conducted trials of fully autonomous vessels in an area off the coast of Den Helder in the Netherlands, completing several challenging nautical tasks to determine how systems interact with other seagoing traffic. The trial tested the capability of the autonomous system to avoid collisions with other vessels on a bridge simulator as well as onboard ships, and show that manoeuvres could be completed and carried out in a safe manner.
“We do not have the intention to develop the technology in this project but more to find out where the technology is mature and where we need to have developments,” said Marnix Krikke, the project’s innovation and human capital director.
“An essential result of the project is the exploration of the use of a simulation environment in proving the robustness and safe operation of autonomous technology.”
The consortium is now planning to set up a large-scale project involving an autonomous short-sea vessel sailing along the Dutch coast.
Ship design and regulation
One advantage of autonomous systems, envisaged by the industry, is the ability to explore new means of ship building and novel ship design. With the ability to remove the human factor from control of the vessel, a number of possibilities open up.
Of particular relevance for longer deep-sea travel is the potential to increase cargo space by replacing crew quarters or other facilities on board required for human transport.
“We will potentially see more efficient cargo stowage, since the accommodation block could be removed – reducing weight, occupied space and optimising vessel lines to improve profile, wind resistance and stability,” says Siem’s Rufus.
Seen as part of a general trend to augment human capabilities with technology, this change may also slowly shift regulatory support towards greater autonomy, lifting restrictions on vessel design that are currently in place.
“At present, the line-of-sight rule limits cargo capacity on some vessels as it requires objects to be visible to the human eye from the bridge,” explains Meling. If we implement new technology, such as camera vision, this gives the opportunity to implement new ship designs with greater capacity, such as additional layers of containers or storage.”
“One area where autonomy may really impact logistics is in the ability to apply multi-modal thinking and open up new and more flexible possibilities for transhipment” – Pia Meling, Massterly
None of these changes is likely to take place until global regulation catches up, however. One fundamental piece of legislation currently standing in the way of autonomous shipping is the International Convention for the Safety of Life at Sea, which requires that all vessels be manned.
“The safety and regulatory environment is not currently set up to accommodate remote controlled or autonomous vessels. Class and statutory regulations do not have provisions for unmanned vessels,” notes Siem’s Rufus.
While flag states may offer individual exemptions to minimum safe manning requirements, in nearly all cases vessels are required to have safety management systems that include certified crew onboard, and as such ships designed without space for any crew will be extremely limited in their operating area.
In the opinion of Höegh’s Bøthun, “Further collaboration and focus on [regulation] is required to move in the right direction at the speed necessary [so as] not to fall behind other competing industries. Shipping should be in the forefront and take advantage of the efficiency gains, cost savings as well as the safety and security opportunities that are there to be harvested.”
Autonomy ahoy?
In the longer term, a move towards more flexible regulation may radically alter not only ship design but operating practices as well, giving operators the option to explore more modular and multi-modal approaches.
“One area where autonomy may really impact logistics is in the ability to apply multi-modal thinking and open up new and more flexible possibilities for transhipment,” says Meling. “At present we see deep-sea vessels docking in port and cargoes then transhipped via short-sea vessel or trucks, but in the future we may see ship-to-ship transhipment where cargoes are transferred from large oceangoing vessels to smaller autonomous vessels outside of port, reducing costs, congestion and distance travelled.”
Given the varied technologies and disparate regulatory frameworks around the world, it seems certain that deployment of autonomous vessels will be piecemeal in the near term. But despite the challenges, it is a matter of when and not if the first autonomous car carriers will be on the water.
“This will be an evolution both in terms of operators’ maturity to test these technologies as well as the regulatory frame conditions that must come into place, says Höegh’s Bøthun.
“We believe that we [will] start out testing manned vessels with augmented decision support for automation and then over time move process by process over to an fully automated and unmanned process. A natural stepping stone is also the land-based operations centre that will help monitor and advise bots and crew.”
“Autonomy is not really something radically new,” Meling explains. “We have been automating processes onboard ships for decades and what we are seeing now is a fusion of well-tested components and systems, like dynamic positioning, sensors and cameras, creating a full situational awareness and ability to have auto manoeuvring and docking of vessels. The transition to autonomous systems will in the future also be gradual rather than sudden.”
Vartdal agrees: “There is a direct evolutionary line from navigational decision support to so-called driver assistance systems that essentially take over navigation with the captain just overseeing the process.”